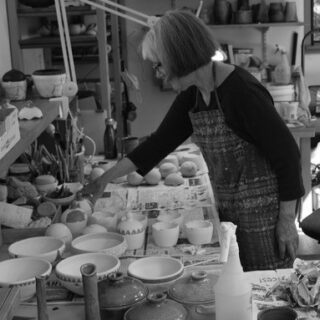
Lovewell, Jan
Alongside her artist husband, Ron Robb, Jan Lovewell has been making pottery in Lund, BC for over 30 years. Her work has been exhibited, published and collected internationally.
The naked raku pottery is formed either by hand or with a wheel; some pieces are altered or impressed with designs. As the pots dry, they are burnished with a stone to make them smooth. They are bisque fired in an electric kiln.
Glaze (temporary) and Firing:
Any areas which will be black are covered with (green) tape. The pots are then coated with a layer of slip followed by a layer of glaze. The tape is carefully removed. Now there are glazed and bare areas on the pot. The bare areas will become black after firing.
The pots are fired to about 1650 F. in a gas kiln. Watching closely, when the glaze starts to bubble, the pots are removed from the kiln with tongs. The sudden drop in temperature cracks the glaze. They are placed in containers with wood shavings, which ignite. The containers are closed and smoke from the smoldering sawdust passes through the cracks, replacing oxygen molecules in the clay with carbon and turning it black. After several minutes, the pots are removed from the containers and submerged in water. This shock helps the glaze/slip layer fall away from the pot. Some scraping, scrubbing, and sometimes, soaking are necessary to remove the shell. After the pieces are clean and dry, they are coated with wax and buffed to protect the surface.
Use & Care:
Naked raku pots are unglazed, low-fired, and because they are porous, are not suited for containing liquids or wet foods. They should be washed by hand. Note: fine crackle patterns can fade after a few years of direct exposure to sunlight.